The Advantage of Plastic Injection Molding
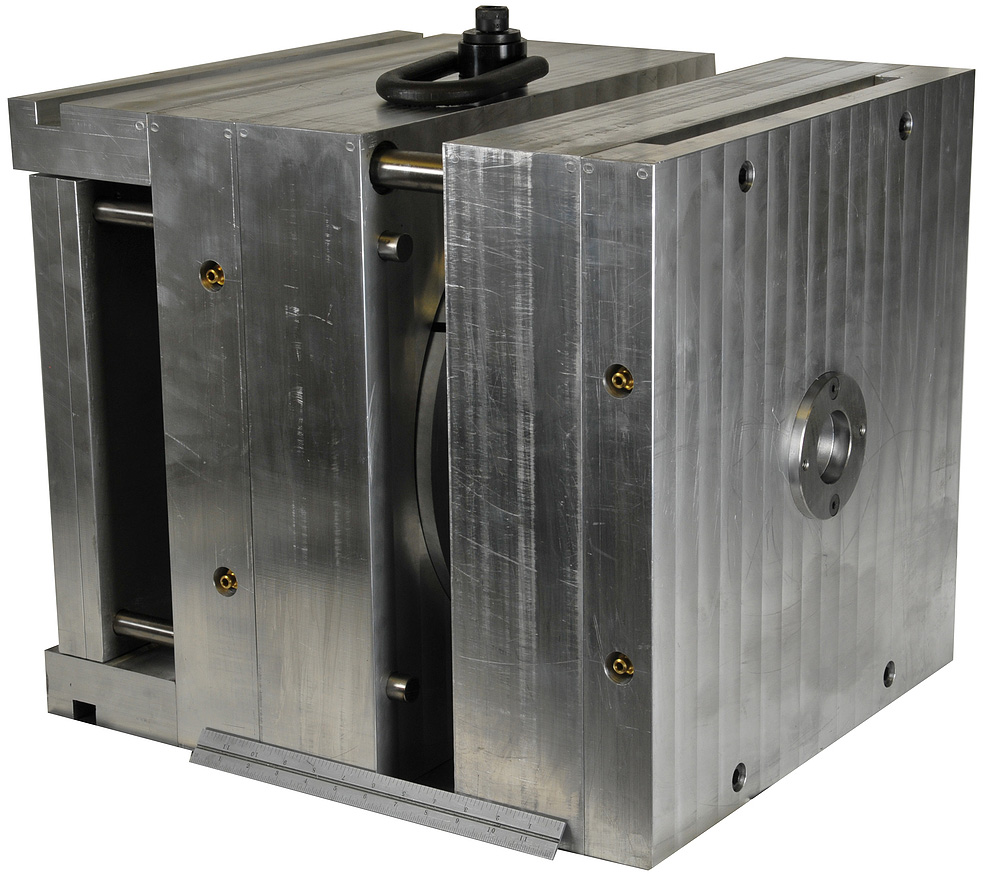
The plastic injection molding process began with metal. The most significant change to the process is plastic instead of metal. Most people know exactly what plastic injection molding products look like, even though they don’t know it. Industrial nameplates, plaques, signs and car emblems are only a few products made through plastic injection. There are a lot of benefits to using the process to create different products.
Versatility and Strength
Plastic injection molding allows you to make complex and intricate shapes that you may have difficulty making by hand. Some components need to be extremely precise and may be more time-consuming, if not impossible to do through manual labor. In addition, the molds last a long time. You use strong, metal molds that you can continuously reuse in future orders. You can expect that each order comes out with the same mold you used before. You can decorate plastic nameplates in as many ways as you want to. For example, you can include metallic foil, texture, UV protection and ink into the mold.
Low Cost and High Volume
If you use traditional methods, you are bound to spend more money. When using plastic injection molding, you create a high volume of products with minimal labor. You do not need manual labor and waste no materials in the process. If you have any leftover plastic, it can melt back down to be used again in a different process.
The machines churn out the same quality items every time. When you have a high-quality mold, you can expect your products to be the same shape, appearance, and quality every time.
When it comes to manufacturing, plastic injection molding saves manufacturers time and money. In addition, it creates a worthwhile product that consumers want. In terms of manufacturing, there are fewer disadvantages to investing in plastic injection molding.